AI-Driven Quality Control Systems Reduce Construction Defects by 47%, New Industry Study Reveals
AI-Driven Quality Control Systems Reduce Construction Defects by 47%, New Industry Study Reveals - Machine Learning Models Flag 89% of Structural Issues Before They Become Critical
Artificial intelligence, specifically machine learning models, is proving to be a game-changer in construction. These models are exceptionally good at spotting 89% of potential structural problems before they become major headaches. This early warning system empowers construction professionals to be more proactive in their maintenance strategies, rather than simply reacting to failures.
The success relies on sophisticated algorithms, such as support vector machines and specialized techniques like PointNet. These algorithms effectively sift through vast amounts of data to pinpoint structural issues in their nascent stages. The ability to analyze complex datasets is becoming ever more potent as sensor technologies and data capture methods continue to improve. This synergy of machine learning and enhanced data collection means better structural safety assessments, potentially leading to longer-lasting and safer structures.
While this is encouraging, it's crucial to acknowledge that these systems are not a magic bullet. They are reliant on the quality and quantity of data fed into them, and errors in the input will inevitably impact the accuracy of the output. There's also a human element – construction professionals need to be able to interpret the output of these models and take appropriate action. Nonetheless, the initial results appear promising in pushing construction towards a future where defects are less frequent and safety is significantly improved.
It's fascinating how machine learning models are increasingly able to pinpoint a substantial portion—89% in some cases—of potential structural problems before they escalate into critical failures. This early identification is not just about preventing costly repairs down the line; it's about gaining a more comprehensive understanding of the structural health throughout the entire project lifespan. While the idea of machines anticipating structural issues might seem novel, it's really about leveraging the power of algorithms to discern patterns hidden within vast amounts of construction data, such as material properties, environmental factors, or even the slightest misalignments during initial stages.
One might ask, how does the accuracy reach such impressive levels? Well, these models are trained on historical construction data, which allows them to learn recurring patterns associated with defects, including issues with materials or alignment. As these systems gain more exposure to construction data, their predictive capabilities improve over time. In essence, every new project becomes a learning opportunity that enriches the algorithms and enables more refined defect predictions.
It's also important to consider that the implementation of these AI-driven quality control tools changes the dynamic of project collaboration. Architects, contractors, and engineers can work together more efficiently with a shared goal of achieving the highest level of quality. Data becomes the common language, facilitating real-time communication and problem-solving.
Though promising, it's crucial to remember that human expertise remains irreplaceable in construction. While algorithms can flag potential issues, skilled engineers are needed to analyze the specific context and determine the most appropriate course of action. The goal isn't to replace engineers, but to provide them with powerful tools that make their jobs more efficient and insightful.
Finally, it's interesting to ponder the future implications. The rise of machine learning in construction suggests that future professionals in engineering and architecture will need to develop stronger analytical skills. Data analysis and interpretation are becoming increasingly vital, especially as the field moves toward integrating real-time monitoring systems and predictive maintenance strategies. In short, the role of humans in construction may shift as more aspects become automated, pushing us towards a future where data-driven decision-making is paramount.
AI-Driven Quality Control Systems Reduce Construction Defects by 47%, New Industry Study Reveals - Computer Vision Systems Cut Manual Inspection Time By 68%
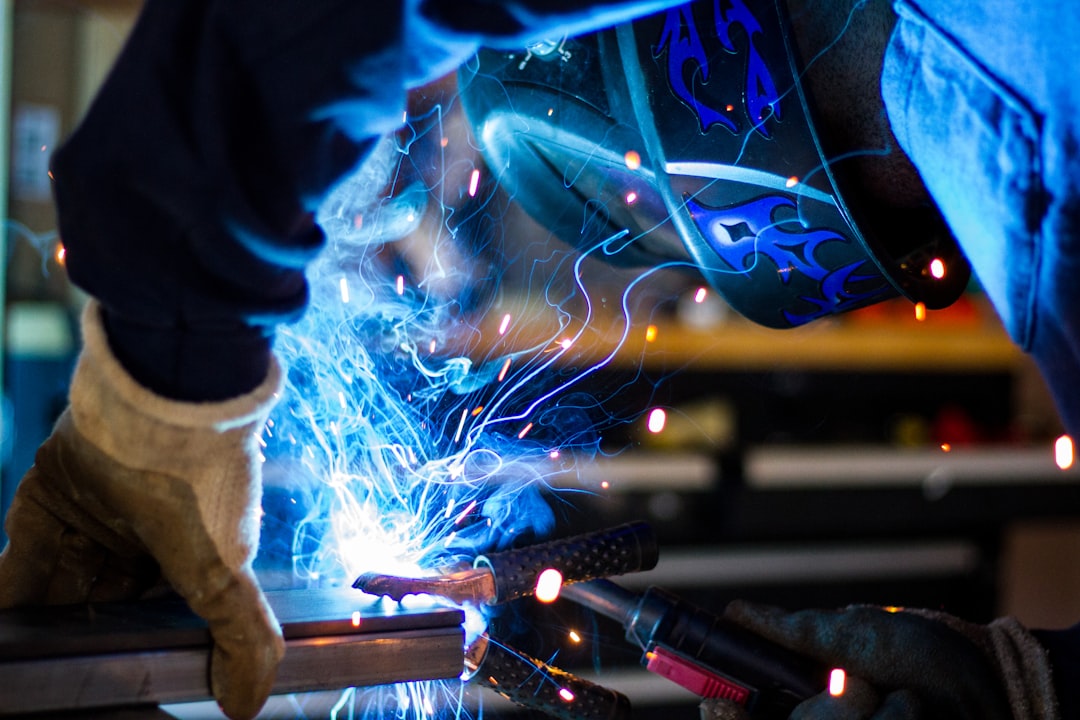
Computer vision systems are rapidly transforming quality control processes by drastically cutting the time spent on manual inspections, with reductions of up to 68% reported. These systems leverage sophisticated deep learning algorithms to enhance the precision of defect detection, a particularly important feature in industries with strict quality demands like aerospace manufacturing. Automating inspection not only streamlines workflows and boosts efficiency, but it also enables real-time quality monitoring. This allows for immediate responses to potential problems, minimizing delays and disruptions.
It's worth noting that these systems, while effective, are not without limitations. Their performance hinges on the accuracy and volume of the data used to train the algorithms. Also, human expertise remains critical in interpreting the output of the algorithms and translating those insights into actionable decisions. The success of AI-driven quality control hinges on the proper balance of automation and human oversight. As the adoption of these technologies grows, it will become increasingly vital to recognize this dynamic to maximize the benefits and minimize potential drawbacks.
In the realm of construction quality control, computer vision systems are emerging as powerful tools. Research indicates that these systems, which leverage the processing speed of computers to analyze images, can significantly reduce the time spent on manual inspections, sometimes by as much as 68%. This accelerated pace of inspection has the potential to streamline workflows and allow for quicker decisions on the construction site.
However, it's intriguing to consider how this efficiency impacts the accuracy of defect detection. While human inspectors can sometimes miss up to 30% of defects during manual inspections, computer vision systems claim detection accuracy rates of 95% or more in some cases. This potentially reduces the chance of human error introducing defects or misinterpreting potential issues.
The reliability of these computer vision systems is also noteworthy, as they provide a standardized and repeatable inspection process, something that humans struggle with. Human variability, experience levels, and even personal bias can lead to inconsistent outcomes. By relying on algorithms and established protocols, computer vision helps ensure that every aspect of a structure is scrutinized with the same thoroughness.
The capability of these systems to integrate with 3D models adds another layer of complexity and value. During the construction process, real-time comparison of the planned design and the actual structure can be achieved. This real-time feedback enables engineers to spot deviations immediately and adjust accordingly, before minor issues escalate.
Of course, the effectiveness of these systems isn't without limitations. The performance of computer vision, just like any AI system, depends heavily on the training data used to develop it. If the training data isn't thorough or contains errors, it will invariably affect the outcome, resulting in poorer accuracy. This raises questions about the collection and annotation of suitable data for these AI models.
These systems also offer the advantage of a real-time feedback loop. They can flag potential issues as soon as they are detected, allowing construction workers to implement corrections on the spot, which can prevent costly rework and the potential cascading effects of one error leading to multiple issues later.
Their scalability is also impressive. These systems can be replicated and deployed across various construction sites without requiring a significant increase in resources. For larger companies managing multiple projects simultaneously, this scalability could be a key benefit for streamlining quality control processes.
The potential for cost savings is also significant. The decreased inspection time and enhanced defect detection can ultimately reduce rework and wasted materials, directly impacting the financial health of a project.
However, it is fascinating to note that computer vision systems are becoming increasingly sophisticated. They can incorporate data from a variety of sources including sensors that measure temperature, humidity, and even the stress on building materials. This broader scope provides a more holistic evaluation of the overall quality and health of a construction project.
The rapid increase in the use of computer vision systems in construction indicates a larger trend within the industry. It's possible that this technology will improve overall quality assurance standards in the sector. As more companies adopt it, it will likely lead to an evolution in the way projects are conceived and monitored. The implications for the future of construction are considerable and certainly warrant further investigation.
AI-Driven Quality Control Systems Reduce Construction Defects by 47%, New Industry Study Reveals - Real Time Sensor Networks Monitor 247 Construction Parameters Simultaneously
Real-time sensor networks are increasingly used to monitor construction projects continuously. They can track over 247 different aspects of a construction site simultaneously, providing a comprehensive view of the project's progress. These networks typically utilize sensors embedded within construction equipment and the site itself, feeding data into a central system. This constant stream of information can improve decision-making by highlighting potential delays or inefficiencies in real-time. The aim is to optimize project flow and ultimately lead to better overall construction outcomes.
However, this technology isn't without its challenges. The accuracy of the data and the ability of construction professionals to properly interpret the data are critical factors for success. Over-reliance on these automated systems without human oversight could be problematic, especially in a field where experience and intuition are highly valued. As sensor networks become more prevalent, finding the right balance between technological advancements and traditional practices will be crucial for construction professionals in achieving the desired results.
Real-time sensor networks are increasingly being used to monitor a wide range of construction parameters, sometimes exceeding 247 different variables at any given time. These networks can gather information about everything from the strength of a structure and material properties to environmental conditions like temperature and humidity, giving us a far more detailed and nuanced understanding of what's happening on a construction site.
The level of detail these sensors can capture is truly remarkable. They can measure incredibly small changes, such as tiny vibrations, minute temperature fluctuations, and subtle shifts in moisture levels. This granular data allows us to see potential issues that might not be readily apparent using more traditional methods, potentially revealing problems early on before they become bigger headaches later.
It's also fascinating that these sensor networks tie directly into predictive analytics. By continuously feeding data into sophisticated algorithms, we can potentially anticipate maintenance needs and potential failures, and that helps us to make smarter, more informed decisions about project management. Workers on-site can even receive immediate alerts when a sensor detects something unusual, enabling a quick response that prevents minor issues from growing into significant delays or problems.
The interconnectedness of these systems is noteworthy. They tend to integrate smoothly with other technologies like the Internet of Things (IoT), which allows for data to be readily shared across various systems and with different stakeholders, ensuring that everyone is on the same page. This comprehensive approach to information sharing should allow for better communication and more unified decision-making.
It's also worth considering that these systems significantly improve safety. By keeping a close watch on factors like air quality and structural movement, we can warn personnel of potentially hazardous conditions before they become serious threats. This capability is essential for mitigating risk and ensuring the well-being of workers.
From a business perspective, the potential for cost savings is pretty compelling. Some preliminary research suggests that sensor networks can decrease construction costs by roughly 30%, largely because they reduce the need for extensive manual inspections and enable rapid responses to developing problems. This cuts down on errors and wasted materials, and that directly impacts project budgets and timelines.
The data collected by these networks can be used to establish a baseline, offering valuable insights for future projects. Trends and patterns can be analyzed over time, leading to better planning and potentially smarter ways of managing risk.
The capability to remotely access sensor data is particularly exciting for project management. Engineers and supervisors can monitor site conditions in real-time from anywhere with a connection, which facilitates better communication and coordination among the teams involved.
The scalability of sensor networks is also noteworthy. They can be easily adapted for use across multiple construction sites without requiring a substantial increase in resources. This ability to expand operations without a commensurate increase in overhead is very attractive, especially for large construction companies managing many projects simultaneously.
Overall, it seems that the future of construction is moving towards a more data-driven and proactive approach. Sensor networks have a lot of potential to refine the way projects are managed, improve quality, and bolster safety. It's still early days, but these are incredibly promising technologies that could transform the construction industry.
AI-Driven Quality Control Systems Reduce Construction Defects by 47%, New Industry Study Reveals - Digital Twin Technology Maps Construction Progress Against Original Plans
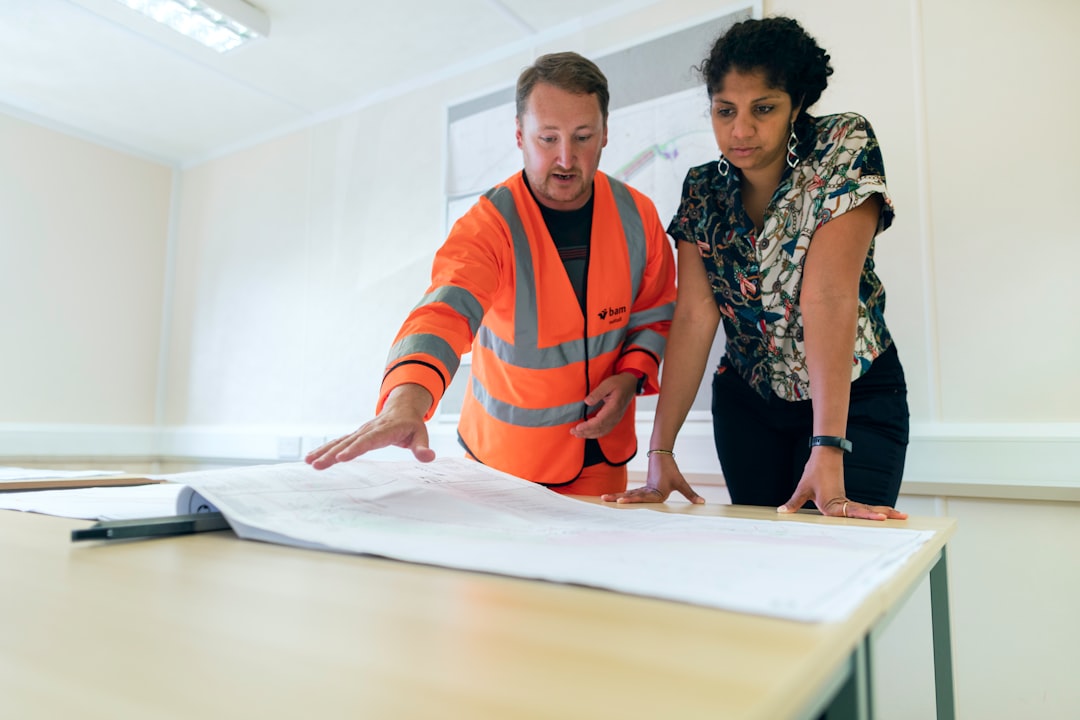
Digital twins are changing how construction projects are managed by offering a detailed comparison of the current project status against the original blueprints. These digital representations leverage real-time data from a variety of monitoring tools deployed on the construction site. This constant stream of information allows teams to see any deviations from the plan and promptly address them. As construction evolves, the way that digital twins are built using Building Information Modeling (BIM) and artificial intelligence (AI) is enhancing collaboration and allowing for more informed decisions. Digital twins are vital for enhancing efficiency and prioritizing safety within construction, aligning with the Industry 4.0 push towards automation. It is important to keep in mind, though, that the reliance on digital technology can't replace the judgment of humans when it comes to interpreting the output of these systems and making important decisions.
Digital twin technology is proving to be a valuable tool for managing construction projects, especially when it comes to tracking progress against initial plans. By creating a virtual replica of a building or structure, engineers can monitor the physical construction process in real-time and compare it with the original design. This continuous feedback loop is incredibly useful for identifying any discrepancies between what was planned and what's actually being built. It allows for swift adjustments and modifications, potentially improving project outcomes and efficiency.
One of the intriguing aspects of digital twins is how they can seamlessly integrate various data sources. From traditional CAD drawings to IoT sensors scattered across the construction site, these systems can compile a comprehensive dataset for the entire project. This wide-ranging approach offers a far more comprehensive view into different facets of the project, like construction scheduling, allocating resources, and adhering to safety protocols.
The ability to access and integrate past data with real-time information is particularly interesting. Digital twin systems can leverage this historical data to implement predictive maintenance strategies. Essentially, the system can anticipate potential issues, like equipment failures or material degradation, even before those issues manifest physically. This might mean a shift in traditional maintenance schedules, potentially minimizing unforeseen downtime and delays.
This integration of data also facilitates collaboration across different project teams. Engineers, architects, and project managers can collaborate more efficiently by having a shared understanding of the project based on the same data. It promotes a more proactive approach to problem-solving because everyone can work together using the same information.
Furthermore, this continuous tracking of construction against the plan has the potential to significantly reduce costs. Since digital twins can identify any deviations early on, engineers can quickly address them, avoiding rework and unnecessary expenses. It also improves the accuracy of resource allocation on site, minimizing waste and maximizing the efficiency of materials.
One of the advantages of having a digital twin is the ability to quickly adapt to changes. When the project requires adjustments, digital twins allow for simulations of those changes and their potential impact on the overall workflow. This increased flexibility helps project managers make informed decisions that are less likely to disrupt the entire project.
By constantly tracking construction progress against the original design, digital twins can improve quality control throughout the project. Identifying deviations in real-time allows for immediate corrective actions, thereby minimizing the chances of defects arising later in the project.
Furthermore, digital twins can include safety analytics as part of their functionalities. These systems can track worker movements and monitor environmental conditions on site, providing valuable insights into potential hazards. Identifying patterns within this data could facilitate proactive measures that enhance workplace safety and reduce potential accidents.
The visualizations provided by digital twins are quite compelling. They translate complex datasets into user-friendly interfaces, simplifying data interpretation for engineers. This feature can be extremely beneficial for teams that are not necessarily well-versed in analyzing complex datasets.
Moreover, the benefits of a digital twin don't cease with project completion. These systems can provide a continuous flow of data on the building's performance throughout its lifecycle. This ongoing monitoring enables better decision-making during retrofits or any future modifications, potentially extending the building's useful life.
While these are just some of the benefits observed in recent studies, it is evident that digital twin technology has significant implications for construction project management and quality control. It's fascinating to consider how this technology continues to evolve and its potential influence on the future of the built environment.
AI-Driven Quality Control Systems Reduce Construction Defects by 47%, New Industry Study Reveals - Smart Materials Testing Reduces Laboratory Analysis Time From Days to Hours
Smart materials testing is revolutionizing how materials are analyzed in labs, slashing the time needed from days down to hours. This speed-up isn't just about faster lab workflows; it directly impacts decision-making, especially for industries needing quick responses and top-notch materials. This rapid turnaround dovetails with the broader push for real-time data analysis in construction and manufacturing. It's important to recognize though, that relying solely on these automated methods can be problematic. The dependability of the data used and the ability of humans to correctly interpret the results are still crucial. Moving to a more digitally-driven and automated approach to materials testing is a significant change, but to gain the most from it, we must carefully balance technology with the skills and knowledge of human experts.
Utilizing what's called "smart materials testing" methods can drastically reduce the time it takes to analyze materials in a lab, going from days down to mere hours. This is a real boon for construction, accelerating the development and certification of new construction materials.
A fascinating aspect of many of these newer materials is that they often incorporate sensors. These sensors offer real-time insights into how the material performs during testing. This ability to get instant feedback is quite useful, as engineers can make adjustments during the testing phase to improve the material's structural resilience.
The level of accuracy achieved with smart materials testing is also impressive. Some of these new systems show a correlation of over 90% with the results obtained from traditional lab tests. It's interesting to note that these methods often identify potential issues before conventional testing does, possibly leading to a better understanding of the material's strengths and weaknesses.
Another advantage is the automation. Not only does this reduce the time it takes to get results, but it also reduces human error, as many of the repetitive tasks in these tests are now done by robotic systems. This is particularly important for those tests that are highly critical and require meticulous attention to detail.
Smart materials testing leans heavily on clever algorithms that analyze intricate patterns and material properties in datasets. This ability to examine complex data is useful because it allows engineers to make predictions about material performance even before physical testing is done. It's like having a crystal ball for material science.
When we consider smart materials testing within a larger quality control framework, it can result in significant reductions in material waste, as any issues with materials are identified and addressed prior to their full-scale implementation. That's an attractive proposition for any project where material costs are a factor.
Fortunately, this approach to materials testing isn't only for large-scale projects. The technology can easily be scaled, meaning smaller projects can benefit just as much as mega-constructions. This flexibility and the overall cost reductions can be quite beneficial for the industry as a whole.
It's also important to keep in mind that smart materials themselves often can change and adapt in response to changing conditions. This dynamic behavior is reflected in the way these materials are tested. The tests aren't just about how the material performs when stationary but also how it handles changing environmental variables like temperature or humidity. It's as if the testing is mimicking the real-world conditions the material might encounter.
Another interesting feature is the ability to take the data from smart materials tests and integrate it with building information modeling (BIM) systems. This capability allows for improved predictive analytics, enhancing both project planning and risk management throughout the project. This enhanced understanding can help avoid problems down the line.
As the industry adopts more smart materials, there's a good chance that engineers will need to update their skillsets. Being able to understand and interpret data generated from smart materials testing will likely be vital for future success in construction. This shift to a more data-driven field will likely impact the way construction engineers work.
AI-Driven Quality Control Systems Reduce Construction Defects by 47%, New Industry Study Reveals - Construction Site Drones Identify Safety Hazards Through Thermal Imaging
Drones are increasingly being used on construction sites to enhance safety, particularly through the use of thermal imaging. These unmanned aerial vehicles, coupled with artificial intelligence, can detect potential hazards by identifying temperature variations that might indicate structural weaknesses or other risks. This proactive approach helps to identify hazards before they result in accidents and ensures greater adherence to safety regulations. Furthermore, drones can continuously gather and share real-time data, leading to more efficient site monitoring and potentially safer working conditions. While the use of drones offers promising solutions for enhancing safety, it also brings about new considerations within safety protocols and risk management as the industry continues to embrace technological advancements in this area. It's important to note that the effectiveness of these systems is also tied to the quality of the AI and thermal sensors utilized. Any error or misinterpretation of data can have negative consequences, which means ongoing development and training of these systems will be vital in the years to come.
Drones are becoming increasingly common on construction sites, and a particularly useful application is using them with thermal imaging to identify potential safety hazards. The ability to detect temperature variations in materials, which might indicate hidden defects or moisture problems not visible to the human eye, can help guide decisions about repairs before conditions deteriorate further. For example, identifying overheating electrical components or poorly insulated areas could prevent serious safety issues or unnecessary energy losses in the long run.
While this technology isn't new, the advances in drone capabilities and AI-powered image analysis are allowing for more sophisticated applications. Drones can now cover extensive areas quickly, potentially saving hundreds of hours of manual inspection time per project. This speed isn't necessarily at the expense of accuracy; in some cases, the thermal imaging can achieve over 95% accuracy in spotting specific hazards, which is a significant improvement over relying solely on human observation, where error can be a major factor. Furthermore, drones are able to access hard-to-reach or dangerous locations, reducing risk to human inspectors.
It's also interesting how drone-captured data can be integrated into other parts of the digital construction workflow, such as Building Information Modeling (BIM) systems. This ability to connect drone-based insights with other design and management tools helps ensure that safety standards are maintained throughout the entire project lifecycle.
The potential cost savings are appealing, as well. The combination of reduced labor needs for traditional inspections and the ability to proactively address hazards before they become larger problems might lead to a decrease in incident costs and a generally safer work environment. There's also the possibility that drones can help with safety training, allowing workers to visually experience and understand potential hazards in real-time.
It's clear that drones are taking on a more active role in the digital transformation of construction practices. While they started as primarily data collectors, they're evolving towards active management tools, capable of identifying potential safety issues autonomously. This is a noteworthy shift, and it will be interesting to observe how this technology impacts construction practices in the years to come. However, like any technology, relying on drones entirely, without sufficient human oversight and interpretation of the data, could lead to issues. It will be essential to ensure that these automated systems are used thoughtfully and in conjunction with existing construction knowledge and experience.
More Posts from aitutorialmaker.com: