AI-Driven Precision Revolutionizing Weight Measurement in Enterprise Manufacturing
AI-Driven Precision Revolutionizing Weight Measurement in Enterprise Manufacturing - Nanoscale Precision AI Algorithms Enhance Weight Accuracy in 2024
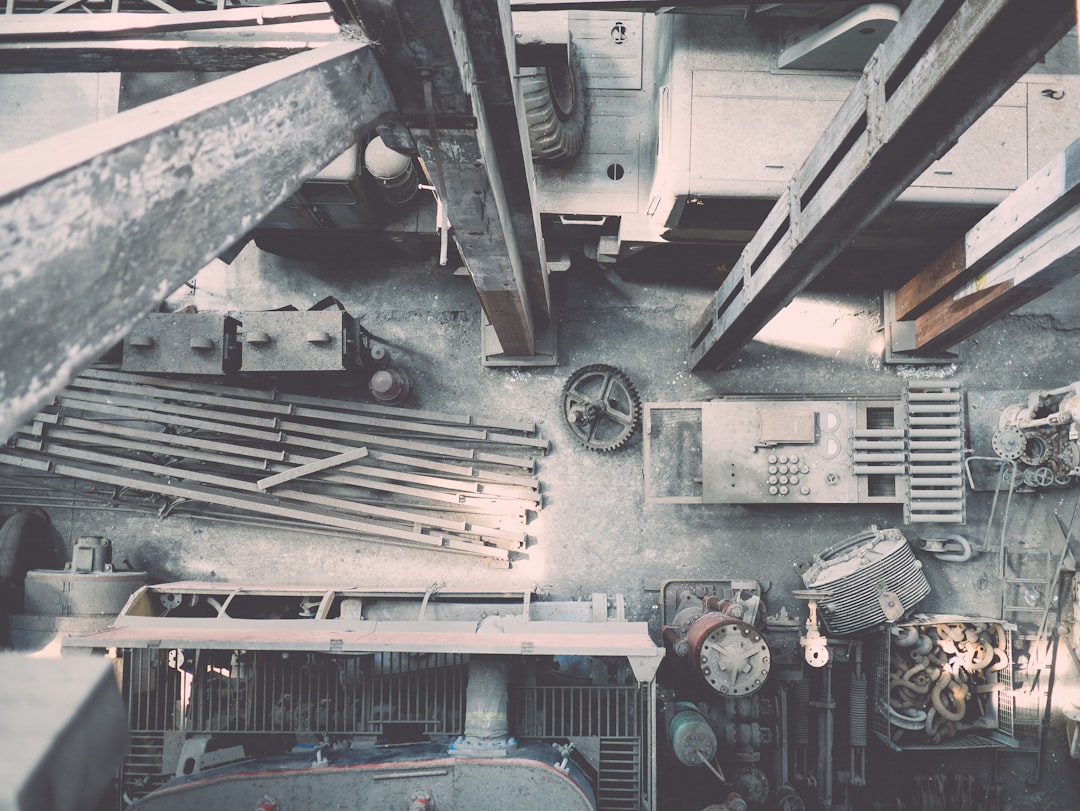
The year 2024 is witnessing a significant shift in weight measurement within manufacturing thanks to the emergence of AI algorithms operating at the nanoscale. This new level of precision, achieved by working at the nanometer level, allows for a previously unattainable degree of accuracy in measuring weight across a variety of manufacturing processes. AI's role extends beyond just measurement; it is being integrated into the development of nanoscale devices and materials, streamlining and improving both efficiency and scalability of production. The blending of AI and nanotechnology offers a powerful approach to redefining how weight is measured in factories, promising more reliable and effective outcomes than traditional methods. However, the full potential of these capabilities is still being explored by various industries, which suggests that the ramifications for standards and practices in precision measurement could be extensive, impacting diverse sectors in the near future. There is debate whether this will truly revolutionize standards or if this is just hype.
It's fascinating how AI algorithms, operating at the nanoscale, are dramatically refining weight accuracy in 2024. We're seeing error reduction down to incredibly small scales, potentially as low as 0.1 milligrams, which is crucial for industries requiring the utmost precision. One interesting aspect is how these algorithms leverage machine learning to dynamically adjust for environmental factors like temperature and humidity—variables that can significantly skew weight readings. This adaptability is a major step forward in achieving reliable results.
Furthermore, predictive modeling within these algorithms is allowing for proactive identification of potential weight discrepancies. Essentially, they're learning from data patterns and anticipating potential manufacturing defects before they arise, which is quite remarkable. Early adopters are already reporting benefits—some companies have seen a 30% reduction in material waste due to the improved accuracy. This is a powerful demonstration of how AI can impact resource optimization.
Another intriguing development is the use of advanced signal processing to minimize noise from sensor data. This is especially vital for applications dealing with intricate, finely machined components. In these situations, even small variations in weight can lead to major failures. Researchers are even exploring combinations of quantum computing and nanoscale algorithms, suggesting that we might soon achieve weight measurement in the sub-microgram range, a truly impressive goal.
Looking beyond immediate accuracy, these algorithms are learning from past weight data, helping to spot gradual changes in product specifications over time. This ability to identify long-term trends allows manufacturers to make preemptive adjustments and maintain consistency. Moreover, the sheer speed of data analysis—thousands of data points per second—is generating real-time feedback that streamlines manufacturing workflows and creates greater operational flexibility.
The implications are significant for sectors like aerospace and pharmaceuticals, which operate with exceptionally tight tolerances. However, achieving widespread adoption will require addressing challenges like standardizing calibration across diverse manufacturing environments. Inconsistencies in calibration procedures can hinder consistent performance across various facilities. While the potential is exciting, standardization remains an important area of future research and development.
AI-Driven Precision Revolutionizing Weight Measurement in Enterprise Manufacturing - Real-time Weight Adjustments Reduce Material Waste by 15%
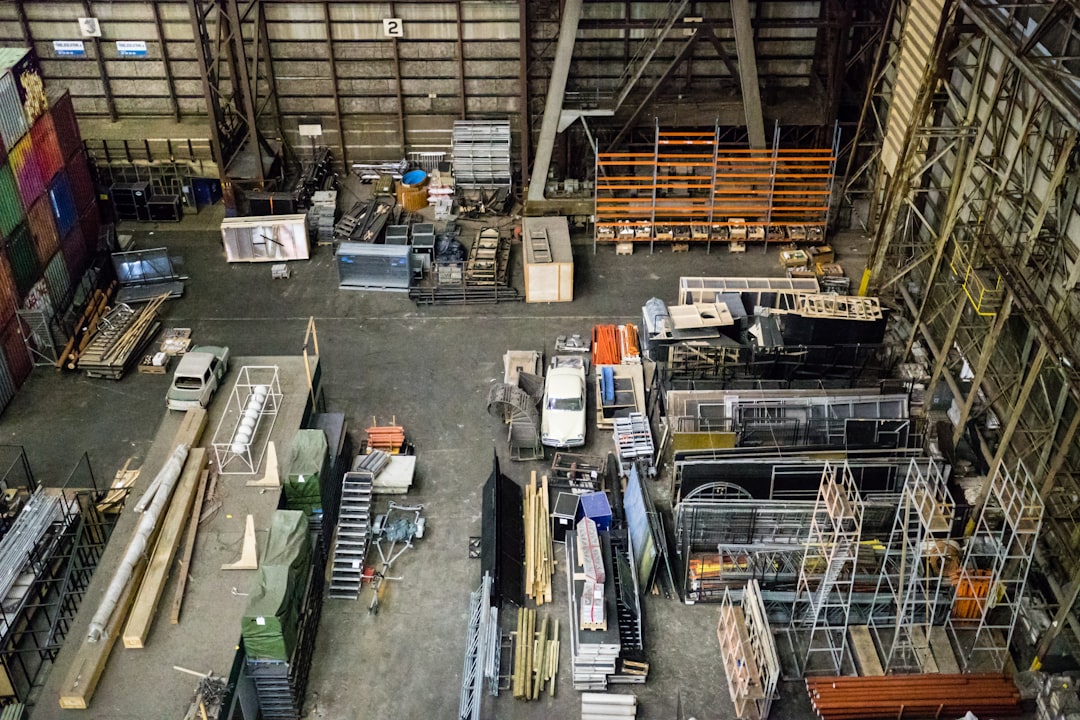
The ability to make real-time weight adjustments during manufacturing is showing promise in significantly reducing material waste, with some cases achieving a 15% decrease. This capability stems from the increasing use of AI-powered precision in weight measurement, allowing for immediate adjustments based on constantly changing data. Manufacturing has long struggled with inefficiency, contributing to a large portion of the world's industrial waste. These new approaches not only help lessen this environmental impact, but also contribute to enhanced product quality and lower production expenses. AI's ongoing integration into weight measurement processes is shaping a future where manufacturing can be more sustainable and efficient. Nevertheless, a significant challenge remains: standardizing these methods across different manufacturing settings. This standardization issue is a key area requiring further attention to ensure that these improvements are broadly applicable and impactful.
Real-time weight adjustments, enabled by AI operating at the nanoscale, are allowing for unprecedented precision in manufacturing, capable of detecting minuscule changes in weight as small as 0.1 milligrams. This level of accuracy surpasses anything previously feasible with traditional methods, which is particularly significant for industries demanding the utmost precision. The algorithms integrate machine learning, dynamically adapting to environmental factors like temperature and humidity. This means that weight readings stay accurate even as conditions fluctuate, which is a big step toward making weight measurements more dependable.
Moreover, predictive modeling within these algorithms is proving useful for proactively spotting potential flaws in manufacturing processes before they create issues. These algorithms analyze historical data patterns and predict possible defects, enabling manufacturers to correct course early on and improve production consistency. Early adopters of this technology have observed a noteworthy reduction in wasted materials, roughly 15% in some cases. It is interesting to note that this aligns with broader research indicating that a substantial amount of waste in manufacturing stems from inaccuracies in weight measurement and poor quality control.
Furthermore, the algorithms effectively minimize noise in the sensor data through advanced signal processing. This is essential for industries dealing with highly precise, finely engineered components, as even tiny discrepancies in weight can have significant implications, potentially leading to significant failures. Research is actively pushing the boundaries further, exploring combinations of quantum computing with nanoscale algorithms, potentially leading to sub-microgram weight measurement, a groundbreaking advancement.
Beyond simply offering a high degree of accuracy, these algorithms analyze historical weight data to identify trends in product specifications over time. Manufacturers gain the ability to adjust procedures preemptively, minimizing deviations from target product characteristics. The incredibly fast analysis speed of these systems—processing thousands of data points each second—results in immediate feedback that simplifies production workflows and makes operations more adaptable.
While this level of accuracy holds incredible promise for industries with stringent tolerances like aerospace and pharmaceuticals, scaling up this technology presents challenges. One hurdle is the need to create consistent calibration standards across diverse manufacturing settings. If calibration methods aren't unified, it can impede consistent results across different factories. While the possibilities are undoubtedly enticing, standardization is a key area needing further research and development.
The increasing capabilities of these AI algorithms have sparked discussion among engineers about the long-term impacts of this technology. Some wonder if these innovations will ultimately reshape industry standards or if they might end up being more hype than a truly revolutionary change. It's a topic that will likely fuel debate in the years to come, as the field continues to mature.
AI-Driven Precision Revolutionizing Weight Measurement in Enterprise Manufacturing - AI-powered Smart Scales Learn from Production Data to Improve Accuracy
Within the realm of manufacturing, AI-powered smart scales are starting to play a more prominent role in enhancing weight measurement precision. These smart scales utilize vast amounts of production data, including historical records and real-time sensor inputs, to learn and adapt, improving their accuracy over time. By processing this data, they can automatically adjust for environmental factors like temperature or humidity, minimizing the impact these variables have on weight readings. This ability to learn and adapt is a departure from traditional weight scales, which often struggled to maintain accuracy in fluctuating conditions.
While the potential benefits are significant, the adoption of AI-powered smart scales within manufacturing environments has been a relatively slow process. Many manufacturers are still in the early stages of exploration, facing hurdles like ensuring high-quality data integration across systems and preparing their workforce for the integration of new technologies. The integration of these systems into existing production workflows also presents challenges, and there's an ongoing debate about whether the expected benefits will materialize in the context of varied manufacturing practices and environments.
The long-term potential of these AI-powered systems for streamlining manufacturing operations, reducing material waste, and enhancing overall efficiency is evident. However, ensuring consistent calibration across diverse manufacturing settings and integrating AI seamlessly into existing workflows remain crucial areas that need further attention. The success of AI-driven smart scales depends on addressing these implementation issues, as well as navigating the complex landscape of production data management and governance. While the initial adoption may be slow, the path towards greater precision in weight measurement within manufacturing holds promise for improving both efficiency and sustainability.
While AI-powered smart scales are showing promise in refining weight measurement accuracy, particularly within manufacturing, several challenges remain. Maintaining consistently accurate data while minimizing disruptions to existing processes continues to be a significant hurdle. For instance, the reliability of weight readings can be impacted by fluctuations in environmental conditions or inconsistencies across different types of equipment.
Furthermore, even with advancements in noise reduction techniques, managing significant disturbances in sensor data remains a challenge. Environments with prevalent vibrations, electromagnetic interference, or simply a lot of activity can make attaining precise measurements difficult. This suggests that integrating these AI systems into existing, bustling factories may require more robust solutions.
The predictive capabilities of these smart scales rely heavily on the quality and quantity of historical data available for analysis. However, many manufacturing operations lack well-established data collection practices, potentially undermining the effectiveness of these AI-driven predictive models.
Creating universal calibration standards across different facilities is another issue that cannot be overlooked. Differences in calibration methods can introduce inconsistencies in measurement accuracy and quality control throughout production lines, consequently hindering overall efficiency.
Moreover, incorporating these nanoscale algorithms into established manufacturing systems can be a complex and time-consuming process. Existing infrastructure may require significant upgrades, potentially leading to considerable financial burdens and delays in adoption.
The learning capabilities of the AI algorithms themselves may not be limitless. It's possible they may reach a plateau in their learning potential after consuming a certain amount of data, prompting a continuous need for updates and input data management to retain their predictive accuracy and effectiveness across diverse operating conditions.
It's also important to acknowledge that the accuracy of AI-powered smart scales is contingent on the quality of the sensors they use. Issues like sensor calibration or drift can introduce errors into measurements, necessitating routine checks and adjustments to ensure reliable performance.
While the real-time processing of data is valuable, limitations in system latency can affect the ability to immediately respond to changes, potentially delaying necessary adjustments within manufacturing workflows.
The use of nanoscale algorithms can be computationally demanding, potentially increasing operational costs related to hardware and power consumption. Striking a balance between performance and efficiency is essential for widespread adoption.
Finally, each industry segment might have its own unique obstacles to overcome when transitioning to AI-driven weight measurement. In the pharmaceutical sector, for example, adhering to stringent regulatory processes may complicate implementation. Finding ways to balance innovation with strict regulatory requirements while maintaining production integrity is a crucial consideration.
AI-Driven Precision Revolutionizing Weight Measurement in Enterprise Manufacturing - Integration of Weight Measurement AI with Enterprise Resource Planning Systems
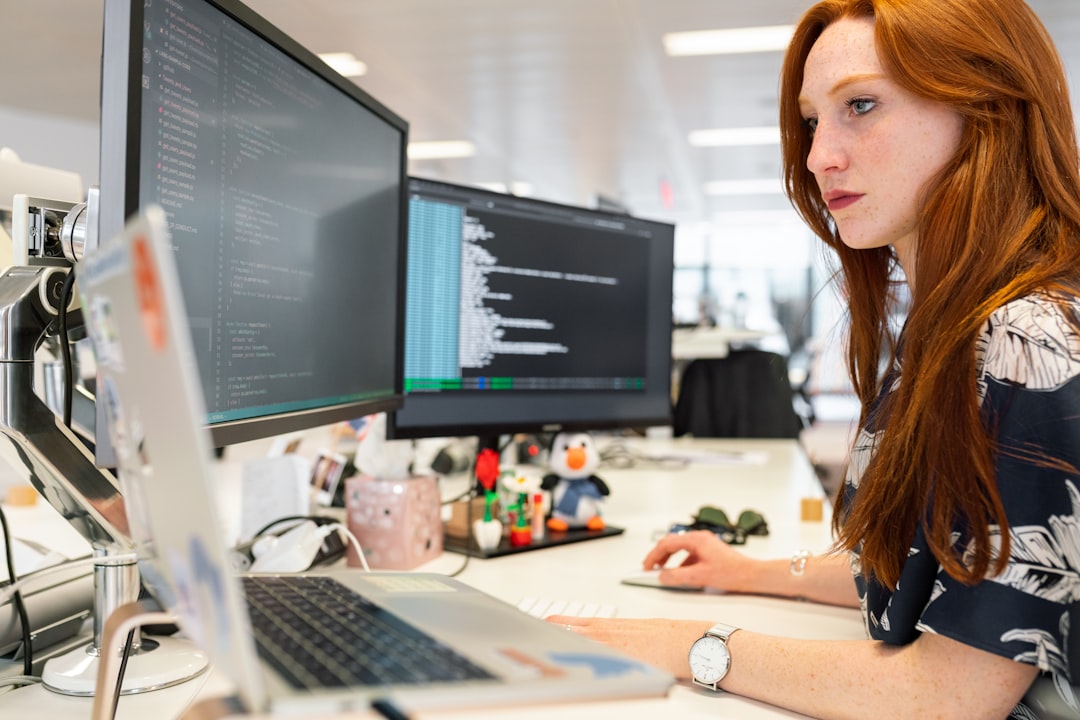
The convergence of AI-powered weight measurement and Enterprise Resource Planning (ERP) systems is reshaping how manufacturers manage their operations. By linking AI's ability to precisely measure weight with the comprehensive data management capabilities of ERP software, organizations gain a more unified view of their entire production process. This interconnectedness brings about improvements in inventory tracking, which in turn can reduce material waste and optimize resource utilization. The integration also unlocks real-time adjustments and the potential for predictive modeling, empowering better decision-making related to production processes.
Despite these positive aspects, there are lingering questions around the practicality of implementing this technology across diverse manufacturing settings. Ensuring consistency in calibration methods across different facilities remains a hurdle, and ensuring that the data integrated with ERP is of high quality is crucial for the success of this integration. It's still a matter of debate whether the benefits of these AI-ERP integrations are substantial enough to overcome these implementation challenges and become widely adopted. As companies continue to experiment and learn, the conversation around the influence of AI-enhanced ERP systems on weight measurement within manufacturing will continue to unfold.
Connecting AI-driven weight measurement systems with Enterprise Resource Planning (ERP) systems is creating a more fluid exchange of data. This integration leads to improved production scheduling and inventory control by connecting real-time weight data to other operational metrics. For example, we can now accurately track and forecast materials needed for production based on their real-time measured weight.
AI algorithms within these smart scales can do more than just measure weight. They can analyze weight signatures and categorize materials based on those unique patterns, leading to more streamlined sorting and quality assurance. This ability to automatically classify materials based on weight alone is a recent development that can potentially speed up production processes.
Integrating AI into weight measurement can lead to quicker production line setups. By leveraging real-time weight data, we can fine-tune equipment calibrations more efficiently, a crucial benefit in highly dynamic manufacturing environments where production can change often. It is interesting to see how much time is saved by automating these tasks.
The ability to automatically adjust for things like temperature and humidity is improving the reliability of weight measurements. But it goes further than that, these systems can now also identify shifts in production procedures and adjust accordingly. It's intriguing how quickly they can make these changes without human intervention.
As AI's role in weight measurement grows, we face questions about data standards needed to make sure different systems can seamlessly work together within a large factory. The issue is that the AI models are learning from diverse machinery types and settings, and we need a way to make sure they can 'talk' to each other.
The enhanced signal processing in these systems helps to minimize sensor noise, but even the smallest interference can create noticeable differences in measurements. This suggests that keeping a consistent and stable manufacturing environment is crucial during especially precise measurements. It makes me wonder if this could limit the applicability of these technologies to certain types of factories.
With real-time data analysis capabilities, manufacturers can track the consistency of weight throughout an entire production run. This means problems can be traced back to specific batches of raw materials or specific parts of the manufacturing process, something that was difficult to do with traditional methods. It's a great advancement in understanding and resolving quality control issues.
The connection between AI and ERP allows for predictive maintenance, using historical weight data to plan equipment maintenance before a problem occurs. This approach reduces the risk of equipment failures linked to variations in weight and enhances the overall dependability of the operation. This kind of integration is a strong example of how AI can be used for preventative measures.
We see ongoing research looking into blockchain technology as a companion to AI in weight measurement. The goal is to increase transparency and traceability throughout supply chains, starting with raw materials and going all the way to the final manufactured product. While still in its infancy, this could be a revolutionary development in logistics and quality control.
Researchers are also exploring how to combine quantum computing with AI for weight measurement. The goal is ambitious—to achieve precision down to the sub-nanogram level. Such accuracy could redefine standards of precision across many industries. It's certainly intriguing to imagine the level of accuracy that this might be able to achieve.
AI-Driven Precision Revolutionizing Weight Measurement in Enterprise Manufacturing - Addressing Ethical Concerns in AI-driven Weight Measurement Practices
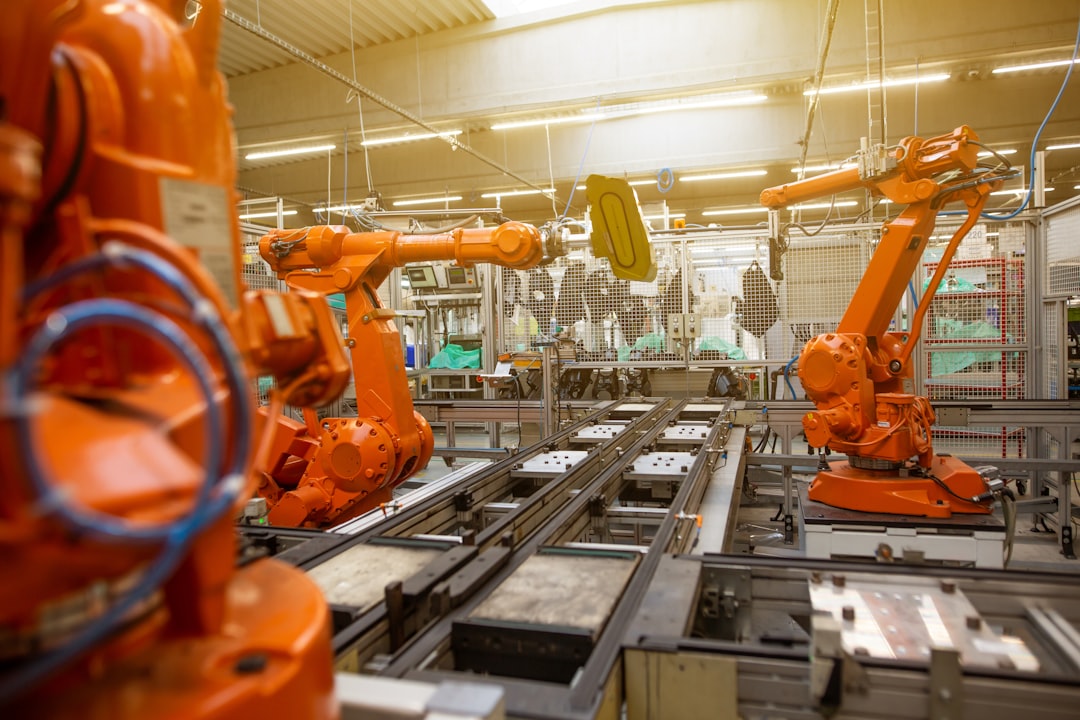
The increasing integration of AI into weight measurement within manufacturing brings into sharp focus a range of ethical considerations. Data privacy, algorithmic bias, and the lack of transparency in AI decision-making are key areas of concern. The potential for misuse of sensitive data is particularly alarming, especially in environments where weight measurements are intertwined with personal information or other potentially sensitive production data. There's a risk that inconsistencies in how AI algorithms are applied across various operational contexts could result in unfair advantages or disadvantages for certain processes or individuals. It is essential to ensure that the development and implementation of AI-driven weight measurement adhere to ethical standards. We must avoid a situation where the drive for innovation outpaces the critical examination of ethical implications. A focus on transparency and responsibility in AI applications will be crucial as companies push forward with new technologies.
The integration of AI into weight measurement, while enhancing accuracy and efficiency, also presents a range of ethical considerations. For example, the vast quantities of production data collected by these systems raise concerns about data privacy, especially when it comes to sensitive information that could potentially reveal proprietary details about manufacturing processes.
Ensuring standardized calibration across different facilities is another critical ethical point. Inconsistencies in measurement protocols could lead to unfair competitive advantages for some manufacturers, while potentially compromising product safety in others.
Many of these AI systems rely on historical data to refine their algorithms. However, a lack of robust data governance could lead to unintended biases within the AI, potentially skewing weight measurement results systematically. We might also see these algorithms perpetuate existing biases in manufacturing if they're trained on data sets that reflect past inequalities in production processes.
Transparency in the decision-making processes of these AI systems is crucial. Without open communication about how these algorithms make adjustments and interpret data, stakeholders may doubt the accuracy of weight measurements and lose faith in the integrity of the production process.
In any automated manufacturing setting, we face the ethical challenge of potential workforce displacement. As AI takes on more tasks, there is a risk of job losses if proper reskilling programs aren't in place to support those affected by automation.
The possibility of unauthorized access to production data through AI systems also creates ethical risks. If not properly secured, these systems could be vulnerable to exploitation, emphasizing the need for robust cybersecurity measures.
Researchers are increasingly calling for ethical guidelines around the use of AI in weight measurement, as a lack of oversight could encourage irresponsible applications with potentially negative outcomes for businesses and consumers.
The sophisticated signal processing techniques used to reduce sensor noise also introduce their own ethical considerations. Stakeholders need a clear understanding of how this noise filtration impacts the reliability of measurements to confidently interpret the results.
Ultimately, the lasting impact of AI on industry standards for weight measurement will depend on how well the industry tackles these ethical issues. Neglecting these concerns could potentially hinder innovation and erode trust in these technologies. It's a balancing act between technological progress and ethical responsibility.
AI-Driven Precision Revolutionizing Weight Measurement in Enterprise Manufacturing - Case Study XYZ Corp Increases Profitability through AI Weight Optimization
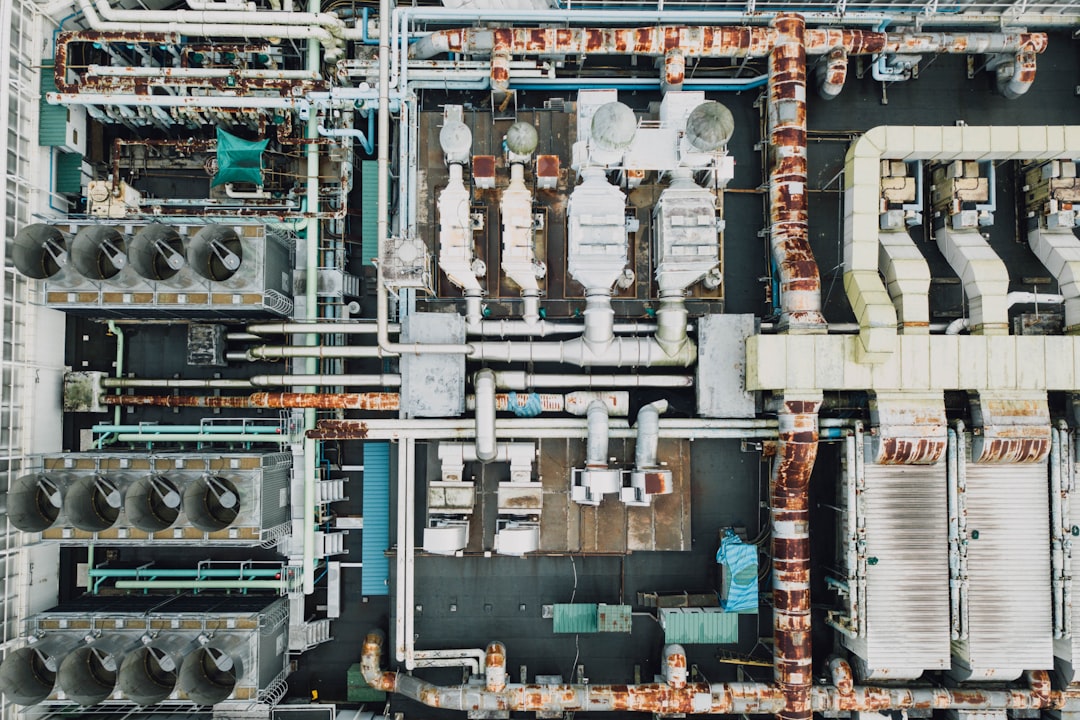
XYZ Corp, a mid-sized manufacturer, provides a compelling example of how AI can boost profitability. They integrated AI for weight optimization, improving operational efficiency and precision in their weight measurement processes. This AI integration led to improvements in inventory management, thanks to more accurate demand forecasting. The partnership between XYZ Corp and Lex Consulting Group was instrumental in implementing these changes, which are projected to boost labor productivity over the long term. While the case study shows positive results, there are still questions about whether this approach can be consistently applied across all manufacturing settings. Maintaining consistent calibration and establishing industry standards are key areas that require attention moving forward. The success of XYZ Corp highlights the ongoing push to integrate AI into weight measurement, showing the potential for innovation, but also raising valid concerns about broader implementation.
XYZ Corporation, a mid-sized manufacturer, successfully integrated generative AI into their operations, which reportedly led to significant improvements in profitability. One of the key aspects of their implementation was AI-powered weight optimization, which boosted their operational efficiency and refined their weight measurement processes. Interestingly, their AI algorithms helped enhance demand forecasting, leading to better inventory management. This project was a collaborative effort with Lex Consulting Group, who helped guide XYZ Corp through implementing these changes.
It seems that analyzing data continuously was a crucial part of improving the efficiency of their AI systems, highlighting the broader applications of AI beyond just weight optimization within a manufacturing setting. There are projections that the generative AI they've implemented will potentially boost labor productivity annually by a small margin (0.1% to 0.6%) through 2040, though whether this will be substantial remains to be seen. It's also worth noting that broader estimates suggest AI has the potential to significantly impact corporate profits globally, with a potential yearly increase of $4.4 trillion across all sectors.
From an engineering perspective, XYZ's focus on AI-driven predictive analytics for managing their inventory was a smart move, enhancing both profitability and overall operational performance. Their approach is noteworthy in the retail manufacturing landscape because it addresses the increasing demand for customized products from consumers. It's quite insightful how XYZ Corporation is positioning itself as a leader in the industry through this innovative use of AI within their manufacturing operations. One wonders, however, how the need for adapting to these changes within a legacy manufacturing environment could impact the workforce long term. It seems the potential benefits might be substantial, but the challenges of successfully integrating this new tech into established practices aren't trivial. We'll be watching how they and others address this going forward.
More Posts from aitutorialmaker.com: