Understanding Kinematic Equations Through Real-World Robot Arm Motion Analysis
Understanding Kinematic Equations Through Real-World Robot Arm Motion Analysis - Forward Kinematics Math Behind Basic Pick and Place Robot Operations
Forward kinematics is fundamental to how basic pick-and-place robotic systems function. It's the process of determining the precise location and orientation of the robotic arm's end effector—its 'hand'—based on the angles and positions of its individual joints. This is much like how our own limbs work, with a series of linked segments (links) and flexible connections (joints) that generate movement. Robotic arms, in their simplest forms, typically rely on rotating (revolute) and sliding (prismatic) joint types.
The Denavit-Hartenberg (DH) parameters provide a systematized way to mathematically represent the relationship between these joints and links. Using DH, we can develop equations that predict where the end effector will be based on joint configurations. These equations are crucial for generating the instructions needed to control the robot accurately. Mathematical matrices help define the spatial relationship of each link to a fixed coordinate system, effectively 'mapping' the robot's physical structure. Ultimately, the math of forward kinematics allows us to convert joint commands into controlled movements, making robotic pick-and-place routines feasible and reliable. This understanding of the fundamental math behind robot movement is important for improving performance in practical applications.
1. Forward kinematics focuses on figuring out where a robot's gripper or end effector is located based solely on the angles of its joints. This core concept underpins a lot of robot motion planning. It's like predicting the hand's position based on the angles of your arm joints.
2. A common way to model this mathematically is using transformation matrices. These matrices essentially describe how each robot segment rotates and shifts relative to the others, allowing us to compute the coordinates of the end effector systematically. It's a bit like a chain of transformations to reach the final location.
3. Robot joints can rotate (revolute) or slide (prismatic), each impacting the kinematics calculations differently. Understanding how these degrees of freedom affect the calculations is essential. Think about how your elbow and shoulder joints allow for different ranges of motion.
4. An interesting output of forward kinematics is the Jacobian matrix. It essentially relates how fast the joints are moving to how fast the end effector is moving. This is quite useful for robot control and analysis. It's a way to understand the relationship between joint speeds and the gripper's speed.
5. The Denavit-Hartenberg (DH) parameters are often used with pick-and-place robots to conveniently describe the robot's physical layout. It provides a standard way to derive the kinematic equations for these types of robots. It's a useful convention for standard robot configurations.
6. The accuracy of pick-and-place tasks relies heavily on accurate forward kinematics. Even small errors in joint angle readings can cause significant positional errors at the end effector. Think about how a tiny error in your arm's angle could affect where your hand ends up.
7. For real-world robot operations, calculating forward kinematics can be demanding, especially with more complex robots with many joints. Optimizing these calculations becomes important for quick, precise movements. If a robot has many joints, it becomes harder to calculate all the transformations needed for forward kinematics.
8. Forward kinematics can help us simulate robotic movements in virtual spaces before actually running them on the robot itself. This gives engineers a chance to foresee and resolve problems in the design phase. This is great way to understand how a robot will perform before physically building and testing.
9. When designing a robot arm, it's essential to consider the workspace it can reach. This workspace is basically defined by the robot's forward kinematics. This influences design decisions like choosing joint types and configurations. This is an example of how the theoretical world of forward kinematics interacts with the practical design world.
10. Intriguingly, the math behind forward kinematics is applicable not just to robots but to other domains like computer graphics and animation. Similar principles are used to simulate realistic and complex movement in digital environments. It's a reminder that the fundamental ideas in engineering can be used to solve problems in seemingly different fields.
Understanding Kinematic Equations Through Real-World Robot Arm Motion Analysis - Understanding Velocity Profiles Through Coffee Serving Robot Movements
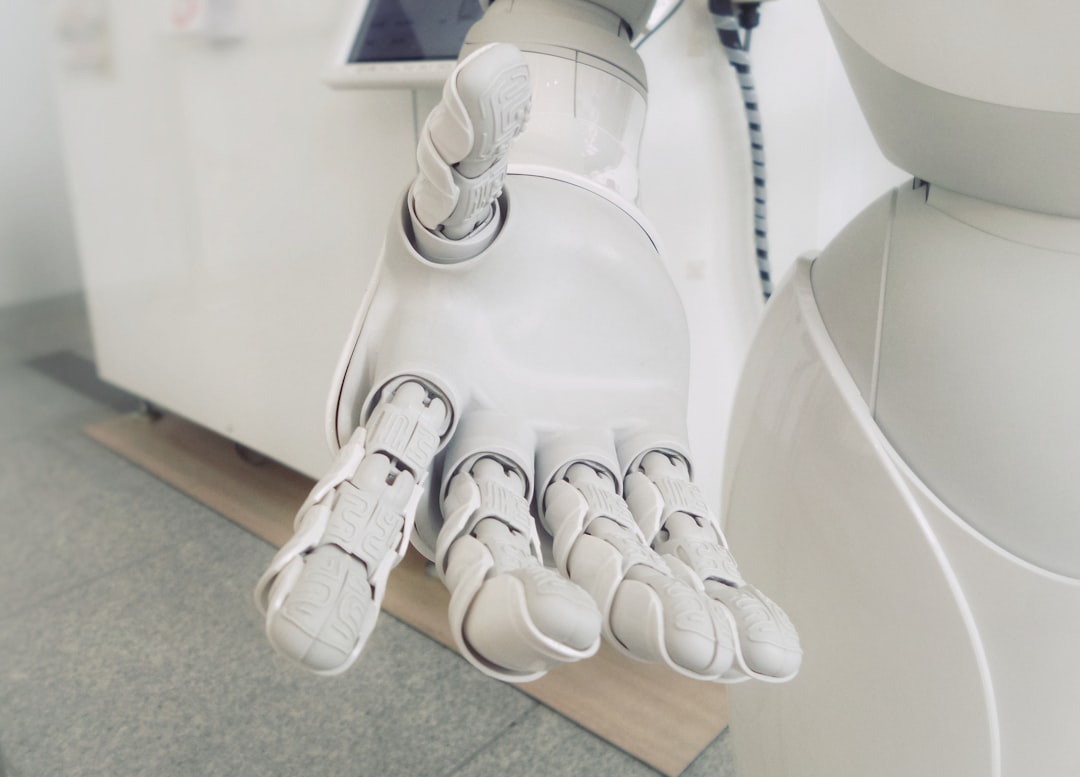
Understanding how a coffee-serving robot moves efficiently requires looking at its velocity profile. This involves analyzing how the robot's arm joints change speed during tasks. We can gain insights into smooth, effective movement by exploring the connection between joint angles and their speeds, often using the Jacobian matrix. These kinematic principles are critical for refining how the robot serves coffee, especially in the development of better motion planning techniques for real-world settings.
Examining the velocity profile in detail can pinpoint areas where the robot's movement could be improved. This analysis can help ensure the robot moves with precision, avoiding problems like overly fast or jerky motions. Ultimately, understanding the role of kinematic equations in analyzing and enhancing a coffee-serving robot's movement underscores their importance in practical applications. While the core concept of kinematics is foundational, a clear understanding of a robot's speed and how it changes is important for building truly useful machines. Unfortunately, simply looking at a robot's velocity is not always the full picture for improving performance as other factors, such as control algorithms, are crucial as well.
Understanding how a coffee-serving robot moves—its velocity profile—is vital for delivering a good cup of coffee. If the robot moves too fast, it could spill the coffee or serve it at the wrong temperature, impacting the quality. Balancing speed and accuracy is key for a smooth, enjoyable experience.
Optimizing robot movements often involves smoothing out acceleration and deceleration using clever algorithms. This helps extend the life of the robot's parts by minimizing wear and tear—a critical factor for maintaining operational reliability over time.
Analyzing velocity profiles helps spot potential inefficiencies in how a robot moves. By understanding when it speeds up or slows down during a serving task, we can potentially identify areas for improvement. It's like watching a video of the robot and identifying awkward or jerky movements that could be refined.
Interestingly, some coffee robots adjust their speed based on how far they have to travel to serve the coffee. For longer distances, they tend to move faster to save time. However, they slow down as they approach the cup, ensuring a more controlled, stable delivery.
Real-time analysis of robot movements reveals how the control algorithms work. By watching the changes in velocity, we can better understand how the robot reacts to changes in its environment. It’s like seeing how the robot’s "brain" decides to adjust its actions.
Advanced robots are starting to incorporate machine learning into their operations. This allows them to learn from experience, gradually improving their serving speed and accuracy based on user feedback or outcomes. It's like watching a robot barista gain experience and finesse.
However, an ideal velocity profile can depend on the environment. A crowded café might require faster, more efficient movements compared to a calm, relaxed atmosphere where a more leisurely approach might be preferred. This means one robot program might not be perfect for all environments.
Some robots utilize feedback from sensors to monitor their end effector's speed. This allows for finer adjustments in real time, even when faced with unforeseen conditions like uneven surfaces or obstacles. This feedback loop helps ensure the robot adapts to its surroundings, making it more robust.
Researchers are increasingly drawing on the principles of how humans move (biomechanics) when designing coffee robots. This can lead to more natural movements, potentially improving both efficiency and user experience. A smoother, more "human-like" serving might be perceived as more appealing.
The study of velocity profiles is not only about improving robot performance, but also about safety. We need to ensure that robot movements don't endanger users or nearby equipment. It highlights the importance of integrating safety considerations into the design of robots and their control systems.
Understanding Kinematic Equations Through Real-World Robot Arm Motion Analysis - Joint Angle Calculations in Industrial Welding Robot Applications
In industrial welding robot applications, calculating joint angles is crucial for achieving precise and accurate movements. These calculations are fundamental to determining the position of the welding tool, or end effector, which is paramount for successful welding operations. However, finding the correct joint angles is not always straightforward. Inverse kinematics, a specific area of robot motion planning, is often challenging because the relationship between joint angles and end-effector position is complex and nonlinear. Adding to the complexity are factors such as the physical tolerances in how the robot joints fit together (joint clearance) and the chain of interconnected links (kinematic chains) that make up the robot arm. Carefully considering all these variables is important for developing reliable and effective industrial robot systems. This level of understanding not only optimizes automation processes but also improves the performance and efficiency of robots operating in industrial settings, where reliability is highly valued.
Joint angle calculations are incredibly important in industrial welding robots. Getting the angles just right is crucial for making high-quality weld beads. Even a small error in alignment can cause problems with the weld's strength and lead to more parts being rejected in factories.
Welding robots often need different kinematic setups compared to robots doing things like picking and placing items. This is because welding involves factors like material warping from the heat and how the metal itself shifts during the process, needing special calculations. Some robots are designed to adjust their joint angles on the fly, using sensors to check the quality of the weld and how the heat is distributed.
The weld joint angles aren't just important during the welding, they're also needed for any inspections after the welding. Inspections frequently have specific requirements for the angle of the welded joints to meet safety standards.
There can be some tricky situations with joint angles, especially in robots with articulated arms. Sometimes, a robot might end up in a spot where it can't easily move the way you want due to the relationships between the joints—we call this a singularity. It's like the robot's movement gets stuck in a specific position.
Welding often involves complex 3D paths. This means engineers frequently use advanced methods like numerical optimization to figure out the best joint angles for each part of the welding process. They try to balance the robot's speed and the weld quality.
When joints are exposed to high temperatures and weld spatter, they need to be made of robust materials and designed well to make sure the robot can still maintain accurate angles. This suggests that the materials and upkeep of the robots are tied to their ability to maintain their kinematic accuracy.
It's interesting that the calculations aren't just about the mechanics of the robot. Some researchers are trying to mimic how humans weld using robot movements. The hope is that this can help develop more intuitive and effective welding processes.
Certain welding applications benefit from using robots with many degrees of freedom, giving them the ability to achieve unusual joint angles. This helps them tackle complex shapes that traditional welding systems find challenging.
The use of artificial intelligence (AI) and machine learning is making welding robots even more adaptable. They can refine their joint configurations by learning from past welding experiences, which then improves both the weld quality and how fast the robots can weld. The robots essentially adapt their joint angles based on past performance to get better outcomes.
Understanding Kinematic Equations Through Real-World Robot Arm Motion Analysis - Acceleration Analysis Using Delta Robot Package Sorting Motion
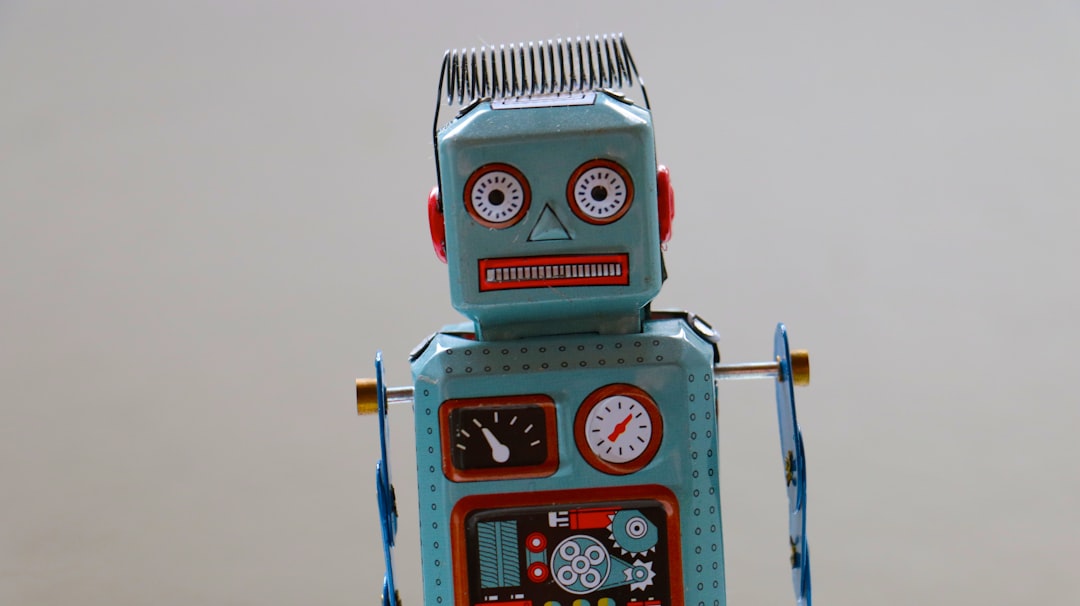
Within the broader scope of analyzing robot arm motion, understanding acceleration becomes crucial when studying the package sorting motions of a Delta robot. Delta robots, widely used in applications demanding speed and precision, like automated warehousing and manufacturing, rely on swift and controlled movements for efficient operation. Analyzing their kinematic equations allows for a detailed look at the acceleration profiles associated with their various motions. This deeper understanding of how the robot accelerates and decelerates during the sorting process helps engineers to optimize the robot's performance and reduce the potential for excessive wear and tear on components. The ability to effectively analyze and predict the effects of acceleration directly translates to enhanced performance and a potentially longer lifespan for these robots across a variety of settings. In essence, studying acceleration within the framework of Delta robot kinematics is fundamental to pushing the boundaries of automation in practical, real-world settings. While a focus on velocity provides part of the picture, the full understanding of a robot's movement requires considering the dynamic aspects of acceleration as well.
Delta robots are frequently used in industrial settings, especially when speed and precision are critical, like in high-speed sorting applications. Their parallel kinematic structure—three arms connected to a base—allows for a wide range of motion while retaining stability, which is crucial for tasks needing accuracy, like sorting packages. Analyzing their acceleration is often done through numerical methods, like integrating acceleration profiles to predict how changes in speed impact performance. This kind of analysis helps anticipate problems like unwanted vibrations or instabilities.
One key challenge with these robots is dealing with the inertial forces that are created during fast movements. These forces can cause unwanted motion or errors unless the control systems are designed to compensate for them, emphasizing the importance of using detailed models. It's interesting how acceleration profiles can be adjusted to reduce energy use. Understanding how speed and acceleration affect efficiency is important when designing energy-saving robots.
However, not all package sizes are handled equally well; bigger packages may need different acceleration settings compared to smaller ones, demonstrating the need for flexible control strategies. Depending on the acceleration, transfer times between locations vary, meaning engineers can fine-tune those parameters to improve output for tasks like sorting items with different weights.
Delta robots are known for their very good repeatability—achieving positional accuracy in the sub-millimeter range, which is important for applications where precise item placement is critical, like sorting pharmaceuticals or electronics. Creating optimal movement profiles for delta robots requires an understanding of jerk, which is how quickly acceleration changes. Keeping jerk low improves the smoothness of the operation and extends the life of the parts, highlighting a crucial area for designers.
The math used to analyze delta robot acceleration can also help to understand dynamics like resonance, which is where specific frequencies can lead to larger vibrations. Engineers need to factor these vibrations into their designs to ensure stability across different operating conditions. This highlights the link between theoretical models and real-world robot design and performance.
Understanding Kinematic Equations Through Real-World Robot Arm Motion Analysis - Motion Planning Mathematics for Collaborative Robot Assembly Lines
Collaborative robot assembly lines increasingly rely on sophisticated motion planning mathematics to optimize their operations. This field involves the application of kinematic analysis to create efficient and safe movement paths for robots working alongside humans. Algorithms like Rapidly Exploring Random Trees (RRT) prove useful in navigating complex workspaces and avoiding collisions with obstacles or workers. Methods like straight-line trajectory planning with interpolation and Task and Motion Planning (TAMP) are crucial for generating smooth and optimized robot movements within the constraints of their physical design. TAMP especially is noteworthy due to its ability to integrate task objectives with kinematic limits.
The use of dual-arm and multi-arm robotic systems presents unique challenges. Designing effective coordination between multiple robot arms demands advanced motion planning approaches to prevent collisions and improve productivity. Moreover, given the shared workspace, safety becomes paramount. This is why many recent studies on robot motion planning focus on creating adaptive models that balance efficiency with the need for robots to react safely and effectively to human operators. It's a challenging field that's constantly evolving as we strive to integrate robots seamlessly into human work environments.
Motion planning for robots working alongside humans, or collaborative robots (cobots), is a complex dance of algorithms and math. One common approach is using what's called Rapidly-exploring Random Trees (RRT). These algorithms are particularly handy for robots that need to find their way through complex environments, basically exploring a vast number of possible paths and selecting the best one, all while avoiding obstacles on the fly. It's kind of like letting a robot explore a maze, trying random routes, until it finds the most efficient one to the exit.
Unlike industrial robots that are usually locked into a fixed routine, cobots are designed for flexibility. This means their path planning must be adaptive, constantly aware of the people around them. As humans move, the robots need to quickly adjust their paths, avoiding any potential collisions. It's a challenging problem, as people are unpredictable and the robot's movements need to change just as quickly.
An intriguing idea in motion planning is the concept of 'potential fields.' Imagine that obstacles are like repelling forces and the desired destination is a magnetic attraction. The robot calculates the optimal path based on these virtual forces, which leads to smooth movements that avoid collisions without strict predetermined routes. This can be advantageous when navigating environments where people are always moving, making traditional path-finding a little cumbersome.
However, motion planning isn't solely about position. Forces and torques also come into play – that's where robot dynamics matter. The robot needs to not only reach its goal but also do so efficiently. This means considering momentum and energy when designing the path, critical for working seamlessly with humans, especially in delicate or repetitive tasks.
Machine learning has also entered the realm of robot motion planning. This allows robots to learn from their experiences. Over time, they refine their paths by avoiding previous collisions or errors. It's like a learning process where the robot gradually becomes better at navigating complex scenarios without human intervention.
Real-time adjustments to robot paths are made possible by control strategies like Model Predictive Control (MPC). This approach allows the robot to anticipate its future position and adjust accordingly as conditions change, a constant dance of optimization and reactivity. This helps balance speed with adaptability, critical in environments where things are always shifting.
Assembly lines can have unpredictable workloads, and robot arms need to respond. This means incorporating how a load affects the robot's movements into the path-planning model. It's like having a model of how the robot changes in terms of how it moves when carrying something heavier or lighter. Without proper accounting, the calculations could become flawed.
Inverse kinematics comes into play when a robot has multiple ways to reach its target. The robot can intelligently select the most efficient or safest trajectory based on its surrounding environment and potential human interaction. For instance, it might be more advantageous to navigate around a worker instead of reaching over them in a tight workspace.
Cobots often use 'safe motion planning' as a priority. This ensures they primarily focus on paths minimizing interactions with humans. Sensors provide real-time updates, so the robot can instantaneously adapt its behavior to ensure safety is paramount. It's like the robot always having an eye on the humans around it.
Finally, managing multiple robots in a shared environment introduces complexities. Coordinating robots involves sophisticated strategies that ensure they are not only following their assigned tasks but are also operating safely and efficiently around each other. The challenges include avoiding congestion, ensuring each robot has the resources they need, and keeping their planned actions synced together. This highlights how a multi-robot system requires more careful management to reach peak performance and safety.
Understanding Kinematic Equations Through Real-World Robot Arm Motion Analysis - Workspace Analysis Through SCARA Robot Paint Application Systems
SCARA robots are well-suited for paint application systems due to their design, which allows them to work effectively within a limited, vertical space. Their four-axis structure provides a precise and controlled range of motion, important for ensuring even and accurate paint coverage. Researchers are continually finding new ways to improve how SCARA robots are used in painting, such as using neural networks to make solving the complex math of inverse kinematics easier. Additionally, some recent designs are attempting to make these robots more versatile by extending the vertical workspace they can reach while also requiring less floor space. The careful consideration of the SCARA robot's workspace is a critical part of optimizing paint application processes. This type of kinematic analysis is valuable in improving efficiency and performance for a variety of real-world scenarios.
1. SCARA robots are particularly well-suited for tasks requiring a compact, vertical workspace, which makes them ideal for operations like pick and place. Their design inherently favors this type of movement, and it can be quite efficient for certain applications.
2. When we analyze a SCARA robot's workspace, we often find unexpected limitations. Things like gravity and the robot's own inertia can affect how smoothly it paints. Understanding these influences is vital for developing good trajectory plans, so we can avoid painting errors and ensure a consistent finish.
3. The speed at which a SCARA robot applies paint is strongly tied to how it accelerates and decelerates. By carefully managing these acceleration profiles, engineers can ensure that the paint applicator maintains a steady pressure, which is crucial for preventing paint drips and achieving an even coat.
4. The rigid structure of SCARA robots and the comparatively smaller number of joints compared to more complex robots, leads to a high level of precision in tasks like painting. This rigidity minimizes flexibility, which translates into straighter and more accurate paint lines.
5. It's fascinating how the workspace of a SCARA robot can be fine-tuned by adjusting the design and limits of its joints. This allows us to adapt the robot to paint more complex shapes. This level of adaptability can lead to improved flexibility in a variety of manufacturing processes.
6. We've discovered that even minor changes in the robot's base height can surprisingly impact the area it can reach while painting. This emphasizes the need for engineers to carefully consider the setup, as it's crucial for maximizing efficiency when painting.
7. When mathematically modeling the workspace of a SCARA robot, we need to consider not just where it can reach but also the orientation of its end-effector (the painting tool). The way the tool is angled impacts how the paint is applied. Therefore, accurate kinematic equations need to account for tool orientation.
8. In painting tasks, the speed of the robot's joint movements can have a surprising effect on the final coat's thickness. It can also alter how the paint dries due to things like airflow and the distribution of heat. This suggests that motion planning needs to take into account the environmental conditions of the painting process.
9. Advanced control systems, like PID controllers, offer a way to refine the painting process with SCARA robots. These systems provide more precise control, allowing for real-time adjustments to keep the robot on the desired path. These adjustments lead to an improved quality in the final painted finish.
10. During workspace analysis, we can identify potential safety problems like the robot overreaching or possibly colliding with other equipment. This type of analysis can help engineers put in place safer operating procedures or design changes to reduce the possibility of these types of accidents.
More Posts from aitutorialmaker.com: