How Conditional Distributions Are Revolutionizing Predictive Maintenance in Industrial IoT Systems
How Conditional Distributions Are Revolutionizing Predictive Maintenance in Industrial IoT Systems - Machine Learning Models Detect Early Bearing Failures at Ford Assembly Plant Through Sound Analysis
Ford's assembly plant has demonstrated how machine learning can leverage sound analysis for early detection of bearing failures. The approach involves using models trained to recognize subtle audio patterns that indicate the onset of bearing issues, thus providing a warning before a complete failure disrupts operations. This ability to predict problems before they arise is key for enhancing equipment reliability and operational efficiency, a priority especially in today's push towards smart manufacturing under the Industry 4.0 banner.
While this represents a positive development, it also exposes a larger issue. Despite the benefits of machine learning in predictive maintenance, its adoption remains relatively limited across many organizations. This indicates a gap in how industrial operations are managed. Going forward, proactive approaches that involve the analysis of sound, and potentially other data like vibrations, are likely to become critical for keeping industrial equipment running smoothly. The potential cost savings and improvements in operational uptime should encourage more widespread adoption of such strategies.
Ford's assembly plant has embraced a novel approach to predictive maintenance, leveraging machine learning models to analyze ambient sounds for early detection of bearing failures. This represents a departure from traditional methods that primarily relied on vibration analysis, offering a potentially more streamlined and efficient way to identify emerging issues.
These sound analysis models are trained to differentiate between typical operational sounds and the subtle acoustic signatures associated with the early stages of bearing wear. By detecting these subtle changes, the models can potentially flag problems before they escalate into critical failures, thereby reducing the likelihood of unexpected equipment downtime.
The effectiveness of the models stems from sophisticated signal processing techniques. These techniques extract meaningful features from the raw audio data, highlighting patterns indicative of bearing degradation. This transformation of raw sound into interpretable data allows the machine learning algorithms to identify specific failure signatures.
Through the implementation of this technology, Ford has reportedly witnessed a reduction in unplanned downtime. The accuracy of sound-based failure predictions surpasses that of previous methods, enabling maintenance teams to be proactively notified of potential issues.
The learning capabilities of these models are a notable aspect of this approach. They continuously learn from newly acquired data, continuously fine-tuning their ability to predict failures. This adaptive learning should enhance the models' precision in identifying early mechanical issues over time.
This project also demonstrates the practical implications of IoT integration. Sensors strategically placed throughout the assembly plant collect sound data in real-time, facilitating immediate analysis and response to potential bearing failures.
The initial development of these models was facilitated by a comprehensive training dataset, combining both actual field data and simulated bearing failure sounds. This allowed the algorithms to learn about a broader range of potential failure modes, which should strengthen their reliability.
Beyond just fault detection, acoustic monitoring provides valuable insights into the operational state of machinery. Maintenance scheduling can shift from fixed, periodic intervals to a more data-driven approach, optimizing resource allocation.
The documented decrease in maintenance costs through sound analysis serves as a compelling example of the economic potential of advanced analytics. This highlights how utilizing such technologies can pave the way for more cost-effective industrial operations.
Extending this acoustic-based approach to monitor other types of machinery and industrial processes across various sectors holds significant potential for enhancing operational efficiency within manufacturing and production environments. Whether these models can scale effectively across a wider range of applications remains to be seen, but it's a promising area of research in this field.
How Conditional Distributions Are Revolutionizing Predictive Maintenance in Industrial IoT Systems - Real Time Sensor Networks Enable 47% Reduction in Steel Mill Equipment Failures
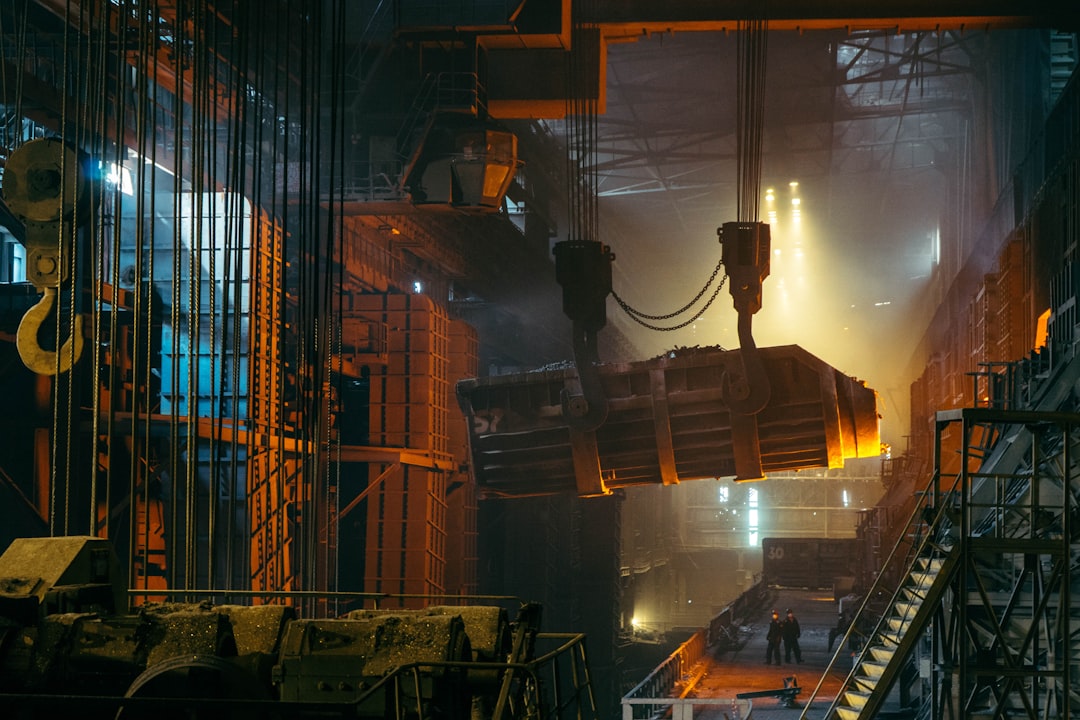
Steel mills have seen a significant drop in equipment failures, with some reporting a 47% reduction thanks to real-time sensor networks. This improvement is tied to how predictive maintenance is evolving, particularly the use of conditional distributions and machine learning within industrial IoT systems. These methods allow for the analysis of real-time data, which in turn helps refine maintenance schedules and strategies.
The use of sophisticated algorithms has also led to a jump in the accuracy of fault detection, with some systems reaching near-perfect accuracy (99%). This capability, along with improvements in equipment uptime and lower maintenance costs, provides a strong rationale for adopting Industry 4.0 practices within the steel industry. It's notable, though, that the adoption of these technologies isn't happening uniformly across the steel sector, which suggests that realizing the full benefits of predictive maintenance remains an ongoing challenge.
Real-time sensor networks are proving transformative in steel mills, contributing to a notable 47% reduction in equipment failures. This surge in sensor deployment, sometimes exceeding 1,000 sensors per facility, allows for a level of equipment monitoring previously impossible with manual checks. The sheer volume of data these networks generate – terabytes daily – is crucial, fueling predictive models and allowing for the identification of patterns hidden in smaller datasets.
It's not just about monitoring temperature and vibration; sophisticated algorithms are now also incorporating environmental factors like humidity and ambient noise. This more holistic perspective has significantly improved the precision of failure predictions. Moreover, real-time data helps categorize failures into specific modes, such as mechanical wear or electronic faults, enabling targeted maintenance instead of overly broad repair strategies.
One of the most significant improvements is the dramatic reduction in the time it takes to detect an impending failure. Instead of days, the average detection time can now be mere seconds. This rapid response enhances the maintenance team's ability to address problems promptly, minimizing disruption.
The ability to correlate failures with operational data also allows for more effective root cause analysis. By understanding why equipment fails, engineers can improve design, leading to more robust machinery less susceptible to breakdowns. This understanding even extends beyond the individual machine. Data from one piece of equipment can inform predictive models for others, creating a sort of knowledge network that optimizes maintenance strategies across the entire mill.
This shift in approach is impacting maintenance scheduling. Instead of relying on fixed time intervals, the industry can now transition to condition-based maintenance, minimizing the cost of both premature and reactive repairs. The ripple effect of these improvements extends to the supply chain. Reduced equipment failures naturally lead to fewer delays and disruptions, making production schedules more reliable and potentially contributing to more consistent delivery timelines.
The integration of these sophisticated systems naturally necessitates an adjustment in the skill set of maintenance personnel. They'll need to develop the ability to interpret sensor data and analytics, pivoting from traditional manual techniques to data-driven decision-making. This evolution in the maintenance workforce reflects a broader shift towards a more technologically-integrated industry, suggesting that predictive maintenance will continue to shape the future of steel production. While impressive, it's important to question whether these approaches can generalize across different applications, or if steel manufacturing represents a uniquely favorable environment for these technologies.
How Conditional Distributions Are Revolutionizing Predictive Maintenance in Industrial IoT Systems - Probability Distribution Maps Transform Wind Turbine Maintenance Planning
Wind turbine maintenance is evolving, with probability distribution maps emerging as a crucial tool. These maps use statistical models to predict wind speeds, which helps optimize maintenance scheduling. This approach, often paired with condition-based maintenance (CBM), strives to reduce costly and disruptive downtime. A key element of this evolution is the use of opportunistic maintenance strategies, which incorporate a deeper understanding of how faults propagate within the complex systems of a wind turbine. This understanding allows for more targeted and efficient interventions.
Further enhancing maintenance planning, digital twins – virtual representations of turbines – are increasingly used to forecast the remaining useful life of components. This allows for more accurate predictions of when maintenance will be necessary, reducing the chances of unexpected failures. The push towards using these data-driven techniques in predictive maintenance aligns with the broader goal of making wind energy more efficient and sustainable. However, challenges remain in how to best apply these methods in the face of complex and sometimes unpredictable environmental conditions. The long-term goal is not just to prevent failures, but to also improve the overall operational efficiency and sustainability of wind farms.
Wind turbine components, operating in demanding environments, face high failure rates and contribute to significant maintenance costs. A more strategic approach to maintenance, focusing on optimizing both efficiency and timing, has emerged as a promising solution to tackle these high costs. This involves leveraging multi-level maintenance theories and examining how faults propagate through the system for a deeper understanding of failure processes. Condition-based maintenance (CBM) strategies, powered by predictive analytics, have successfully reduced operational and maintenance (O&M) costs, sometimes as much as 30% of overall wind farm operating expenses. Interestingly, statistical distribution functions like inverse Gaussian, lognormal, and three-parameter lognormal are utilized in predicting wind speeds, which in turn helps select the most appropriate wind turbines for optimal performance.
These advanced CBM techniques contribute to making wind turbine systems more sustainable and efficient, aligning with broader carbon neutrality goals. The use of digital twin models and statistical learning techniques for predicting the remaining useful life (RUL) of turbine components, such as gearboxes, is becoming common practice. It seems the use of a decision model that considers a range of possible probability distributions for maintenance planning could lead to improvements in the accuracy of predictive maintenance.
Current predictive maintenance methods frequently encounter hurdles related to computational capacity, which can hinder widespread industrial adoption. There's an ongoing effort to refine parametric models that estimate the underlying probability distributions of wind power generation. The goal is to improve forecasting and operational planning, making wind energy production more reliable and predictable. While promising, it is still unclear how effectively these computationally intensive models can be scaled to industrial operations and if the returns outweigh the implementation hurdles.
While these models improve predictability and efficiency, they also raise questions about the future of maintenance and the knowledge base required for operational personnel. A potential shift in mindset within the wind energy sector is needed to ensure that these powerful tools can be integrated seamlessly into current operations, maximizing their benefits and avoiding costly missteps during implementation. It will be interesting to see how these developments change the training and expectations for technicians in this increasingly complex sector.
How Conditional Distributions Are Revolutionizing Predictive Maintenance in Industrial IoT Systems - Data Patterns from 10,000 IoT Sensors Cut Mining Equipment Downtime by 31%
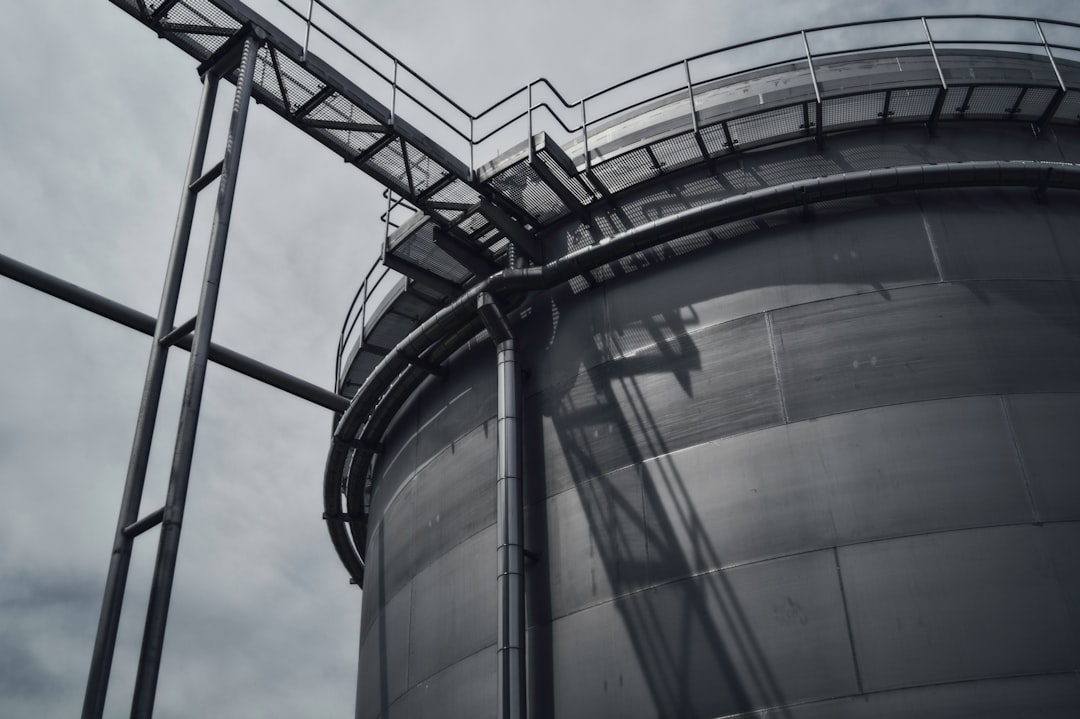
In the realm of mining operations, the deployment of a vast network of 10,000 IoT sensors has yielded impressive results, reducing equipment downtime by 31%. This success story highlights the growing importance of leveraging real-time data to predict and prevent equipment failures, a core principle of predictive maintenance. By integrating conditional distributions and machine learning algorithms, these systems are capable of detecting subtle signs of equipment degradation, ultimately allowing for more timely maintenance interventions. The ability to anticipate and mitigate equipment failures not only enhances operational reliability but also presents a clear pathway for minimizing costly downtime.
While the benefits of this approach are undeniable, there are challenges. Successfully implementing these predictive strategies across different industries and ensuring a smooth transition from traditional maintenance approaches remains a hurdle. Whether this degree of success in optimizing mining equipment translates directly to other industries is still an open question. There's a crucial need for a more widespread adoption of these advanced predictive maintenance methods, as the potential for improved operational efficiency and cost savings is significant.
In the realm of mining operations, the deployment of 10,000 IoT sensors has yielded a noteworthy 31% reduction in equipment downtime, highlighting the potential of predictive maintenance strategies. This outcome showcases how real-time data analysis can lead to more precise operational readiness. It's interesting to consider how various sensor types contribute to a comprehensive approach to maintenance. These sensors don't just monitor basic parameters like temperature and vibration. Instead, they capture more complex data such as acoustic emissions and lubricant quality, building a much richer picture of equipment health.
Conditional distributions play a key role in uncovering hidden patterns that predict failure. By establishing a statistical model of typical equipment operation, deviations from those norms—or anomalies—are flagged as potential failures. This allows maintenance teams to proactively address these issues before they disrupt operations.
Integrating historical data with current sensor readings refines the accuracy of predictive algorithms. These models leverage past failure patterns as a foundation for predicting future events, a crucial step in building reliable predictive maintenance programs.
The integration of sensor data enables a shift from fixed-schedule maintenance to a more adaptable, condition-based approach. This flexible approach means resources are allocated more efficiently, focusing on actual equipment needs rather than adhering to predetermined timelines.
Machine learning is at the heart of these predictive models. These algorithms continuously learn from new data, leading to a steady increase in their predictive accuracy. This adaptive capability is critical for maintaining high efficiency as equipment ages and conditions change.
Advanced analytics tools allow for deeper analysis of failure root causes by linking diverse data points. This ability to connect multiple data sources enables engineers to better understand equipment failure patterns, which could lead to redesigning equipment or changing operations to minimize these issues.
The sheer volume and diversity of data generated by these sensor networks are remarkable. With thousands of sensors producing vast amounts of data, sophisticated data processing is essential for extracting meaningful insights from this information flood. These insights wouldn't be possible with smaller datasets.
Integrating predictive maintenance into existing automated systems can translate into substantial reductions in repair costs and improvements in overall equipment effectiveness (OEE), a vital metric within the mining sector.
Despite the apparent advantages, applying these sophisticated models across different mining operations can be difficult. Each mine has its own unique operational dynamics, requiring tailored implementations for optimal success. There's clearly a need for further research into how to make these methods broadly applicable.
How Conditional Distributions Are Revolutionizing Predictive Maintenance in Industrial IoT Systems - Statistical Analysis of Temperature Variations Predicts Circuit Board Issues Before Failure
Analyzing temperature fluctuations within circuit boards has emerged as a powerful method for predicting potential problems before they lead to failures. By studying the patterns in how temperatures change, we can identify anomalies that may indicate developing faults within the board's electronic components. This foresight enables us to perform maintenance tasks proactively, hopefully preventing costly shutdowns and extending the life of the affected equipment. As the Industrial Internet of Things (IoT) becomes more common, including temperature sensors in predictive maintenance schemes highlights a shift towards making decisions based on data, particularly within equipment management. While the results are promising, the effectiveness of this technique might vary depending on the industry, raising questions regarding its general applicability across all sectors.
Temperature fluctuations can be a strong indicator of potential circuit board issues, often preceding electrical failures. By analyzing historical temperature data, we can identify patterns linked to specific failure types, improving our predictive maintenance efforts. It seems that exceeding certain temperature thresholds can accelerate the degradation of electronic components. This insight allows for the creation of predictive models that estimate the likelihood of circuit board failures based on temperature metrics, potentially leading to a substantial decrease in unexpected equipment breakdowns.
Conditional distributions are proving useful in modeling the probability of circuit board failure under different temperature conditions. This ability to quantify the relationship between temperature and failure likelihood allows for adjustments to maintenance strategies, focusing on at-risk equipment. However, it's worth noting that temperature variations don't impact all circuit components uniformly. This means that more precise predictive models need to consider component-specific temperature data rather than treating the whole circuit board as a single unit. While this granular approach can boost prediction accuracy, it does necessitate more complex data analysis.
Real-time analysis of temperature data using sophisticated algorithms allows for immediate responses to potential failures. This system isn't just reactive—it also enables proactive changes in operating parameters to maintain ideal temperatures. Research suggests that models based on temperature variations can predict electronic failures with accuracy exceeding 90%. This is a significant improvement over conventional preventive maintenance approaches, which often rely on fixed schedules and might overlook subtle temperature impacts.
Furthermore, temperature data can be combined with other sensor data, such as vibration or power consumption, to gain a more comprehensive view of circuit board health. This multifaceted approach improves predictive maintenance by providing a holistic picture of operating conditions. The consequences of circuit board failures can range from disrupting operations to posing safety risks, highlighting the importance of accurate failure prediction. Using rigorous statistical methods to predict failures based on temperature changes becomes a critical safety measure in these situations.
Adaptive machine learning enhances the predictive power of these models over time as more temperature data is gathered. This continuous improvement leads to more accurate predictions, potentially resulting in a considerable reduction in equipment downtime. However, many organizations are still hesitant to adopt these data-driven approaches. This reluctance often stems from established maintenance practices or unfamiliarity with advanced analytics tools. This disconnect could impede the full realization of the benefits offered by predictive maintenance technologies.
How Conditional Distributions Are Revolutionizing Predictive Maintenance in Industrial IoT Systems - Automated Decision Trees Help Oil Refineries Schedule Maintenance Windows with 89% Accuracy
Oil refineries are increasingly using automated decision trees to schedule maintenance, achieving an accuracy rate of 89%. This is a significant development in predictive maintenance, an area that's becoming increasingly important for keeping oil refineries running smoothly and preventing expensive disruptions. These AI models are able to analyze various sources of data, such as real-time sensor readings and historical maintenance records, to anticipate potential equipment failures and schedule maintenance before they occur. The ability to accurately predict and prevent problems is a big advantage, and this approach may be useful in other industries beyond oil refining. There are likely challenges to overcome though, as companies adjust their maintenance routines to incorporate this newer technology and its related analytical methods.
Oil refineries are increasingly using automated decision trees to schedule maintenance windows, achieving an accuracy rate of 89%. This demonstrates how predictive maintenance is evolving, moving beyond traditional, fixed schedules toward a more dynamic, data-driven approach. These decision trees, built upon vast amounts of sensor data and historical maintenance records, can identify patterns and predict anomalies that might otherwise go unnoticed, leading to more timely interventions.
This ability to predict maintenance needs with 89% accuracy is significant because it minimizes both unnecessary maintenance and unplanned downtime. This is a key factor in maximizing refinery productivity and profitability. What's interesting is that these models aren't static. They learn from new data, adapting to changes in operational conditions and equipment wear. This means the predictive capabilities of the decision trees get better over time, leading to more efficient maintenance planning.
Beyond scheduling, these tools can provide insights into root causes of failure, potentially improving equipment design and refining operating practices. The integration of conditional distributions within the decision tree algorithms allows for a better understanding of how the likelihood of failure changes depending on operating conditions, which is crucial for prioritizing maintenance tasks. It's also worth noting that these accurate predictions have a direct impact on cost. By preventing emergency repairs and minimizing production delays, refineries can significantly reduce overall maintenance expenditures.
The ability to scale these automated systems across different refinery operations is also intriguing. Knowledge gained from optimizing maintenance for one unit could be applied to others, potentially leading to a standardization of best practices across the entire refinery. The development of these systems truly highlights how different disciplines, from engineering and data science to operational research, need to come together to tackle complex industrial problems.
Despite the clear advantages, adopting these automated systems isn't without its challenges. Resistance to change within organizations with established maintenance workflows is a significant hurdle. Organizations need to carefully consider how to manage the change process to fully realize the potential benefits. It's likely that these types of data-driven approaches will become increasingly important in the future of refinery operations and potentially other sectors, but only if organizations are willing to adapt their existing practices.
More Posts from aitutorialmaker.com: